Schneider Electric completes its first UK Smart Factory
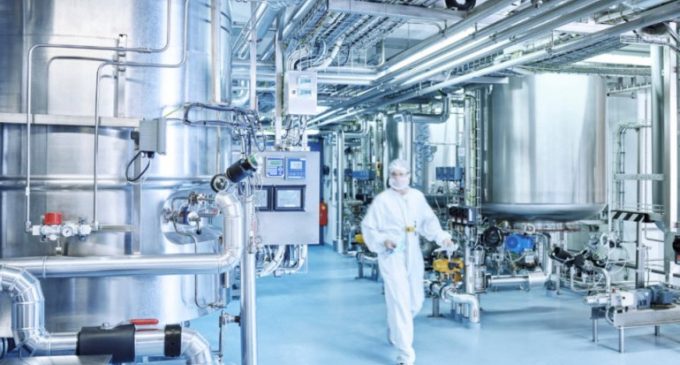
Schneider Electric, a leader in the digital transformation of energy management and automation, and AVEVA, a global leader in industrial software, have digitally upgraded their factory in Flint, Wales. The project, commenced in late 2018 and costing £300,000, will see the site become the UK’s first Schneider Electric smart factory.
The SMART transformation project primarily involved retrofitting the existing factory to maximise efficiency and minimise downtime. The hardware solutions deployed were complimented by the the full EcoStruxureTM software suite including Facility Expert, Resource Advisor, Machine Advisor, Augmented Operator Advisor, and AVEVA insight.
The combination of digital tools, unified by EcoStruxure™, provide the facility managers with the ability to control and optimise every aspect of the factory. Facility Expert enabled managers to keep a digital logbook of equipment and rapidly identify and respond to any problems within the production site, Machine Advisor provided machine analytics to empower operators with the ability to optimise machine operations and improve reliability, while the AVEVA platform acted as a visualisation platform for continuous operational improvement and real-time decision-making support.
Schneider Electric’s investment was paid back within just one year, thanks to productivity and a range of efficiency-based savings. Maintenance costs saw a 15% reduction (£91,000) due to the installation of a Lean Digitisation System (LDS) system with Andon alerts and an additional £14,000 in savings thanks to the installation of Intelligent Lighting Systems onsite.
In turn, efficiency at the Flint factory was greatly enhanced. Despite a 20% decrease in demand in 2020 due to COVID-19, Flint’s operational efficiency improved by 5% compared to 2019 levels and productivity increased by 4% – the latter represents £240,000 in savings alone. In 2021, operational efficiency is set to increase a further 7%.
The transformation also had a range of sustainability benefits. Water consumption was halved – down from 4228m³ in 2019, the highest of any site in the UK, to 2138m³ in 2020, with projections of just 960m³ in 2021. Likewise, improvements to efficiency associated with the installation of variable speed drives, smart panels, and other technological solutions led to a 15% decrease in electricity (KW/h) usage compared to 2019 levels.
Beyond the hardware and software introduced to the site, staff were empowered to become more aware of areas of inefficiency and take ownership of issues. They now have instant access to dashboards, as well as the ability to create alerts to notify them of any changes within the plant.
Mark Yeeles, Vice President of Industrial Automation at Schneider Electric, said: “From a production and maintenance perspective, the factory used to be digitally blind. Over the course of a few years, we have become the first smart factory in the UK with complete operational visibility and clarity. We have control over real-time processes and can achieve a higher level of sustainability and safety. Given the project achieved a ROI within a year, it’s been an undeniable success for all involved.”
Enrique Herrera, Industry Principal for Manufacturing at AVEVA, said: “Flint is a fantastic success story in all aspects – safety, productivity, and sustainably, at a reasonable cost. The fact that the site saw a return on the investment in smart technology within just a year and dramatic decreases in water and electricity use is testament to the potential for manufacturers to transform the way they operate quickly, cost-effectively, and sustainably. It also demonstrates the continued success of AVEVA and Schneider Electricity’s strategic partnership, which has gone from strength to strength.”