Aseptic Fill/Finish – A Market Shift Toward Small Scale Batch Processing
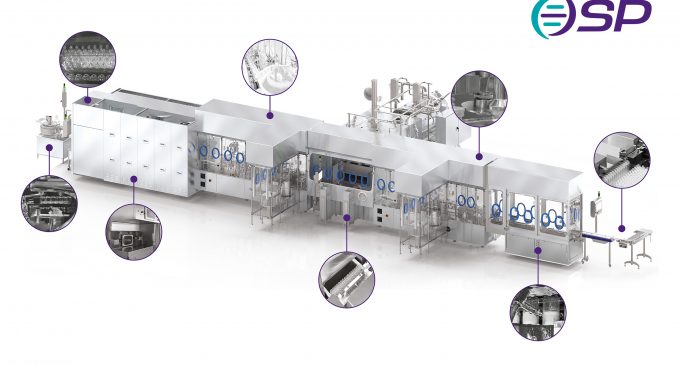
Compared with a decade ago, the role of biopharmaceutical manufacturing has evolved considerably.
Where the early 2000’s to 2010 placed larger emphasis on larger scale, higher throughput processing, contemporary market demand now centres on a need for more specialised treatments and targeted therapeutics – all of which facilitate a push toward smaller batch sizes during the manufacturing stage.
Equally, CapEx tenders no longer fixate on the need for larger footprint equipment capable of processing high volumes of product. Instead, present day tenders / projects desire smaller and more flexible system solutions, to meet the needs of a highly versatile market space.
However, despite this notable shift, it is generally acknowledged that rather than abating, process regulation continues to maintain, and in some cases, increase in stringency level. This is largely due to, regardless of throughput, the rigour with which aseptic fill/finish biopharmaceutical manufacturing must satisfy the highest of regulatory standards and compliance – falling short and non-compliance is simply neither an option, nor something the regulatory bodies will tolerate.
To achieve this paradigm shift, in terms of a meeting a reduction in batch throughput, manufacturers have undergone a significant evolutionary process. An example of this being manufacturing facilities segregating their floorplans/sections to ensure their capability to build multiple versions of highly versatile smaller scale CapEx equipment in parallel, are maximised.
Another interesting observation is of the need to manufacture not only small scale, fully GMP compliant equipment lines, but the individual elements of the line, where requested.
Flexibility remains a key driver pushing the fill/finish market, so the need for manufacturer’s to offer a smaller throughput vial washer that can fit on to a pre-existing de-pyrogenation tunnel or liquid filler is also of paramount importance. The mantra of today no longer emulates that of a decade and more ago, whereby one size – i.e. higher throughput – fits all.
Please refer to the image below for a greater insight into the small layout currently demanded by companies and operators:-
In terms of overall benefits to companies, operators, and engineers alike, these can be itemised into the following categories:
- Footprint
- Machines can be installed with minimal space requirements, as opposed to their higher throughput cousins
- Companies are able to free up area in their facility, to accommodate other process equipment, and thus maximise their available laboratory or clean room use
- Equipment Designed for Purpose
- Operators are able to run small batches on instruments designed for smaller throughputs for better efficiency, rather than utilise much larger instruments to work on scales equating to a fraction of the overall capacity
- Machine operation costs are reduced as largely over-sized instruments are no longer needed to be powered up and used for batch sizes far lower than the operating capacity of the system
- No Compromise on Quality
- As previously mentioned, despite the smaller footprint and speed, this has no impact on the GMP compliance associated with the unit
- From a Quality and Engineering Department perspective, a series of machine validation options are available, with supporting documentation to confirm the provenance and performance of the equipment
- Extremely high process parameters, such as high accuracy liquid filling and check weighing for example are maintained
The trend toward this more efficient processing method and equipment is beneficial not just to manufacturers bottom line, but to the end users as it helps ensure that when sterile injectables are administered to patients, product efficacy, and patient health/safety are in no way compromised
To discover more or discuss your requirement, speak to a BPS Crowthorne product specialist today. Visit www.bpscrowthorne.ie
You may also be interested to watch these videos:
- What does a filling line capable of processing 50 vials per minute look like in practice?
- What does a vial journey look like? Here’s a full fill-finish solution in action!