Smart moves on the factory floor
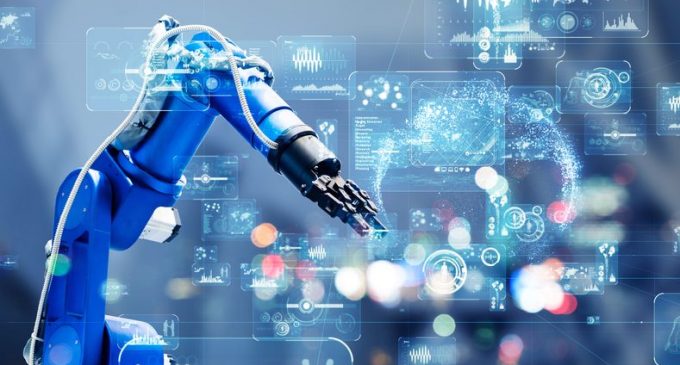
It’s all change in the manufacturing industry, with automation, artificial intelligence and augmented reality coming to the fore. Rockwell Automation is helping Irish manufacturers bring intelligence to the process
Most Irish people probably don’t think about the country as a manufacturing centre. However, while it is true that the country was not an industrial powerhouse during the 20th century, hammering out cars or planes (though it did long have Ford and Volkswagen plants), Ireland today is home to a number of vibrant manufacturing verticals – all of them high-tech.
Pharma, medical devices and semiconductors lead the way, alongside food and drink production and agri-food.
It’s a growing area, too: according to figures from the Central Statistics Office, the value of products manufactured and sold by Irish-based enterprises rose by 7.1 per cent to €121.4 billion in 2018. The pharmaceutical sector alone accounted for €47.8 billion.
Interestingly, growth has continued even as the country faced the coronavirus pandemic. Manufacturing production in Ireland increased 5.9 per cent in April of 2020 over the same month in the previous year.

J J Condon, Country Sales Director for Rockwell Automation
J J Condon, country sales director for Rockwell Automation, said that Irish manufacturing is in rude health.
“I think there’s a pretty broad base of manufacturing in Ireland and there’s been a significant evolution in recent years. The largest is life sciences, and that breaks up into pharma and medical devices. In second place there’s consumer packaged goods (CPG) and food and beverage, and then the agri.
“We’ve also got semiconductor with the likes of Intel and pockets of niche industries, with mining equipment built in Tyrone,” he said.
Rockwell Automation, a global supplier of industrial automation and information solutions with significant operations in Ireland, sees Ireland as a growth market and is working with clients to bring more and more intelligence to the manufacturing process.
Different sectors are driven by different factors, but all of them see the benefit in smart manufacturing.
“What you typically find is the end product drives the focus on automation. In [both] bio processing and bulk pharma you have manufacturers motivated to lower costs, but more importantly to maintain quality. In food and drink it’s because it’s a highly competitive industry,” said Condon.
Indeed, Condon said that the growth of some sectors was notable – such as Irish whiskey, which, after lagging for years, is now challenging the Scotch whiskey market as a high-value export product.
“Look at the evolution of Irish whiskey in recent years; a lot of the success of Irish whiskey has come from enhanced process automation,” he said.
Automation is about more than moving to the robotic technologies that we might recognise from the past. Today, it can mean being right out on the cutting edge.
As an example, Rockwell Automation has developed augmented reality (AR) solutions in high-value pharma production.
“In the likes of bio pharmaceuticals it has been driven by the need for ‘right first time’ batch set-up. We’re working with companies like GE Healthcare, now called Cytiva, to optimise the single batch, using technologies like AR to help get it right on bioreactors.
“In a single-use process operation there’s approximately 600 points of connection that operators have to set up. That’s a pain point and you’re still relying on a human to do it. We have an operator working off a tablet and it prompts the operator, identifying the components,” he said.
Among Rockwell Automation’s clients are blue chip life sciences businesses, including, beyond pharma, noted medical device manufacturers. Naturally, each producer will have its own requirements and goals.
“Some are using technology to directly drive a better product, while others are working on the production processes, such as driving to reduce downtime as efficiently as possible,” said Condon.
Data capture
Increasingly, Rockwell Automation’s job is to capture data and move it from the factory floor for analysis that can be fed back down to the manufacturing process.
“All of these components link into the data streams within the facility. Rockwell has partnered and significantly invested in a company called PTC. Using data analysis software has allowed us to take information up into the IT layer of the businesses from the operations layer,” he said.
This has not always been common, and silos have developed that Rockwell Automation uses information to break through.
“Predominately it’s because they’re just different folks; IT people are not like operations people, but there’s also been a question of security,” said Condon.
Typically, Rockwell first engages with customers via its own in-house consultancy group.
“We want to find out what the pain points are. They might be maintenance issues [but] it can also be energy: a big driver for customers now is energy conservation and sustainability,” said Condon.
In all cases, though, manufacturers, those most physical of businesses, are keen to move forward with digitisation, said Condon.
“Every company we engage with now is talking about a digital roadmap or a digital journey. I’ve never seen such consistency from everyone I’ve been speaking to,” he said.
“We also find that customers’ demand for support on the ground is always there, and we work with our partners to deliver that. Having local support is very important.”
The coronavirus pandemic has shown one key advantage of digital transformation: it vastly increases flexibility, something that was seen when Irish manufacturers got to work producing essential supplies.
“In general, in manufacturing, what we saw straight away was a lot of companies quickly retooled to address a corporate social responsibility. We saw some producing ventilators, we saw Irish Distillers in Cork use alcohol to make the [hydro-alcoholic] hand gel.”
This may seem a one-off, and we all hope it is, but such flexibility has clear uses. Discussion about rapid vaccine and treatment production, for example, is already under way.
Rockwell is working with customers to adapt how people move within their facilities to maintain social distancing.
“We’re able to map and optimise the flow of people,” said Condon.
“The first step is simulation, working with end-users to look at the process flow of people. The second step will be the implementation of that, which will require RFID or sensors to manage that.”
Condon said that, looking beyond the pandemic, the move toward digitisation is the key conversation being had.
“It’s about more flexibility in the manufacturing process. We saw that in retooling to make ventilators, but also in bespoke manufacturing, the ‘batch of one’. One of our customers is 3D printing [limb] joints, bespoke for the individual. Personalised medicine is an area of significant growth,” he said.
Looking forward, manufacturing, with its advanced deployment of cutting-edge IT, could find itself at the forefront of the economic recovery from the pandemic and lockdown.
“It’s a challenging time for manufacturers, but it’s an exciting time because of the technologies,” said Condon.
Reference: BusinessPost.ie