Combilift coping with Covid
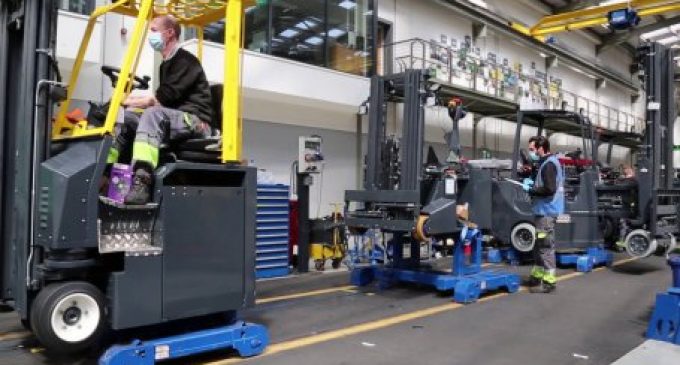
Irish material handling solutions provider Combilift has implemented a number of measures to keep up its productivity in times of Covid-19 and social distancing – its space optimisation expertise has also proven to be invaluable for customers.
When Ireland went into lockdown, Combilift’s operations were classed as essential. Despite this, the company decided to suspend production for three weeks. Martin McVicar, ceo and co-founder, explains how this decision allowed time to prepare a series of measures to protect employees and continue operations as close to full productivity as safely possible.
The number of employees on site at any one time was reduced from 600 to approximately 350. With those working operating on a two-shift rotation as opposed to a single shift. It has also segregated its the 46,500 sq m manufacturing facility into eight segments.
“Our biggest challenge was how to keep social distancing measures in the staff canteen areas” McVicar said. Eight individual canteens were set up, and employees are taking staggered breaks to make social distancing possible.
Thermal cameras at entry and exit points in the facility have been set up. “This non-intrusive device sends an alert to the HR department if a member of staff is suspected to have a high temperature,” McVicar explained.
This myriad of measures, alongside the use of facemasks, hand sanitiser stations strategically placed around the facility and the installation of copper covers on door handles, have so far allowed Combilift to operate at 90 percent productivity.
Combilift installed copper covers on door handles in its facility
Productivity has also been a top priority for Combilift’s customers – particularly in the manufacturing sector, which has to get back to normal output levels while creating extra space in production areas so that employees maintain safe distances from each other.
It addition to its range of multidirectional forklifts, pedestrian stackers, aisle master articulated trucks and straddle carriers, the Irish manufacturer offers a free warehouse layout and material flow consultation services to ensure that customers make the best possible use of their space. This expertise has proven to be invaluable for customers aiming to maximise production areas; by optimising these areas companies can comply with safety requirements whilst maintaining output.
Pre Covid-19, the global manufacturer would usually conduct plant visits both domestically and internationally. Due to travel restrictions, it is instead conducting virtual site surveys using platforms, namely WhatsApp, to virtually ‘walk’ through the facility with the customer.
Combilift said that it has received positive feedback from these video consultations, and it is often more convenient for the customer also. “The turnaround time can actually be faster, and the customer is under no cost obligation,” said McVicar.
Reference: www.heavyliftpfi.com